前回までで基板設計、発注と、回路側の準備が終わりました。
今回は電子回路やスイッチを組み込む筐体、外側の箱を設計・作成していきたいと思います。
-
-
【自作】PICマイコンで赤外線学習リモコンを自作する③:基板設計・組み立て
前回までで試作したマイコンボードを用いたソフトの作成・デバッグが完了しました。 完全にバグは消えていませんが・・・・・ 今回は試作した基板を参考に、から完成形の基板を作っていきたいと思います。 基板を ...
続きを見る
筐体を設計してテストパーツでチェックする
今回もいつも通り3Dプリンターで筐体を作成してみました。
基板は実物がすでにできているので、適当にノギスで寸法を測りつつ図面に起こして設計しています。
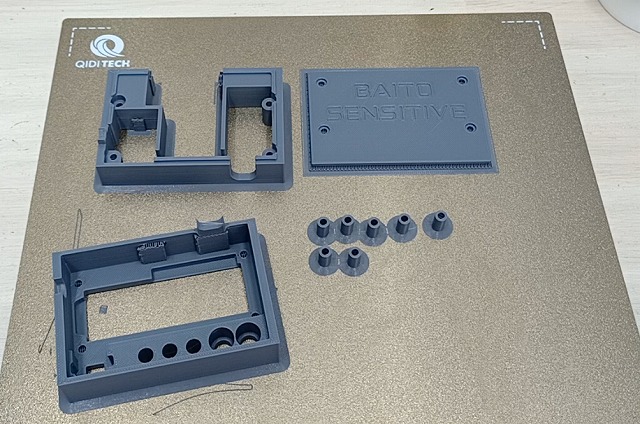
そこそこ3Dプリンターは使っていますが、なかなか一発で設計できないんですよねぇ・・・・
自分の場合、だいたい4~5ステップはほぼ確定で生じてしまいますね・・・・
①だいたい寸法を測ってテストパーツを印刷
↓
②中に入れるパーツ類を組み込んで合うかどうかテスト(100%合わない。一発であったためしがない)
↓
③再度修正して印刷、テスト
↓
④ほぼあうが、どこかしら不満点や不都合がある
↓
⑤再度修正して印刷、テスト
↓
⑥完成。
本音を言えば一発で成功させたいんですが、これはなかなか経験が必要になりそうです。。。
頭の中でどことどこが干渉する想像力とか、これじゃ印刷後の材料の縮み分できつくなるとか、
そういうノウハウをもっと蓄えないとですね・・・・
そもそも、完璧な3Dモデルを作らず現物の基板の寸法を測りながら作っているのが一発でうまくいかない原因だと思いますが、手を生画化して作っているほうがイメージわきやすいんですよね。。。。(多分人による)
ミスプリントするたびに「材料もったいないなぁ~」と感じてはいますが、やり方はしばらく変えないと思います。
そしてまぁ、例にもれず、いつも通り、見事に干渉いたしました。
赤外線LEDの発光部分に穴が開いているのですが、思ったより真ん中からずれていたせいで2個のLEDのうち一個しか出ていないです。
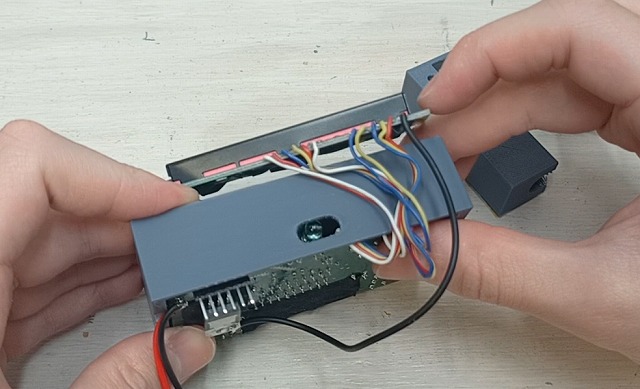
これだけでなく、LCDディスプレイ上部のはんだ付け部分とケーブルも干渉していました。
今回購入したLCDディスプレイは表と裏の両面にランドが出ているのでどちらからでもはんだ付けできるのですが、
なぜかケースに入れる方向のランドにつけてしまったので、ケースに入れるときに干渉してうまく入らないです。
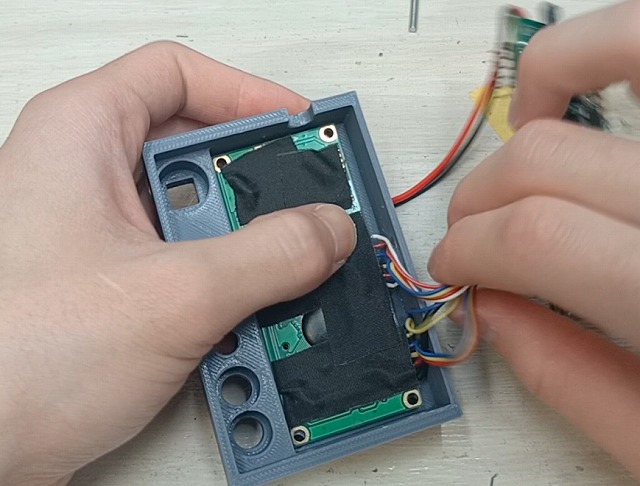
この辺の干渉を取り除くように、設計寸法を修正して再度印刷しなおします。
筐体を再設計、完成版を印刷する
せめて再印刷は1回で済ませたいところ。
基本的に3Dプリンターで印刷した材料は再利用できないので、寸法が間違っていた時点でゴミ確定です。
海外の動画でプリント済みのパーツを溶かして再度フィラメントとして使う、というのを見たことがありますが、ほこりがフィラメントに混入したりしそうなので正直やりたくないかな・・・(アイデアとしては理想ですが。。。)
自分の中で3D設計のルーティンが固まっていればいいんですが、毎度行き当たりばったりで思いついたまま設計しているで、一発で成功させるのが難しい状況です・・・・
それでも一番最初、5年前に授業でCADに触った頃よりは格段にレベルアップしている(と、信じたい)ので、数こなして慣れていくしかないかな~と感じてます。
印刷が終わったら、パーツの出来を見ていきます。
今回もきれいに印刷できました。
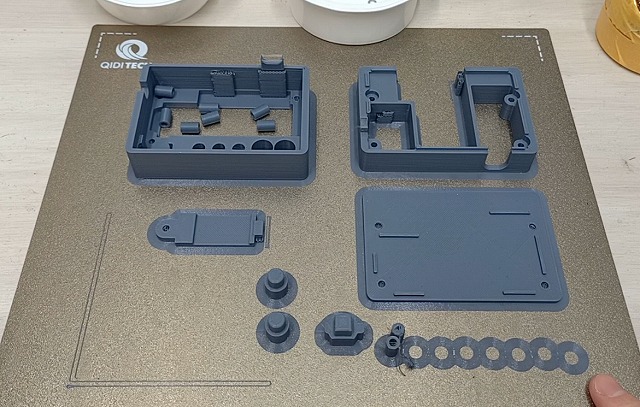
一応本番印刷なのでビルドプレートにスティックのりを塗りましたが、やって後悔しました。
印刷物がベタベタして気持ち悪いです。
そのそもこのビルドプレートで印刷中にはがれたことはほとんどないので、やらなくてよかった気がします。
今回使用したプリンターは下記のものですが、QIDIのビルドプレートはかなり優秀なのでお勧めです。
-
-
【3Dプリンター】QIDI Tech X-PLUS3 がやはり最高だったのでレビューする
今回は3Dプリンタを更新した話です、 前回購入したものが非常に安定した動作、安心なサポート体制だったので、今回も同じメーカーから購入しました。 4年ぶりの3Dプリンタ更新! 今回4年ぶりに3Dプリンタ ...
続きを見る
印刷物がとてもはがしやすいのに印刷中ははがれないというなかなかいいやつです。
ビルドプレートだけでもこのメーカーのものを使った方がいいんじゃないかと思うぐらいには性能がいいです。
加工の名称がいまいちわかりませんが、ヨーグルトのフタの裏のようなザラザラした加工になっています。
ビルドプレートから部品がなかなか離れない場合はスクレーバー等を用いることが多いと思いますが、ビルドプレート自体にダメージが入りやすいので正直微妙。
だんだんビルドプレートが削れてきてななめになっていくので、造形時に3Dプリンターが正しい軸だしをできていたとしても積層痕が残りやすくなります。
できるだけ軽い力で印刷物をはがせるビルドプレートをお勧めします。
出来上がりチェック
はがした印刷物は以下の通り。
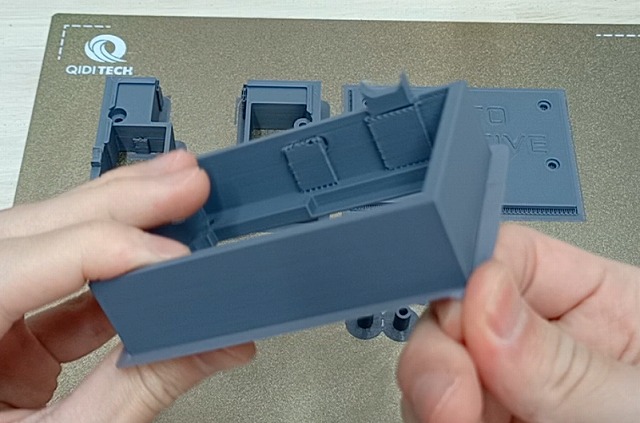
ビルド面がザラザラしているので固定面がどうしてもザラザラしてしまいますが、正直どうでもいいのでやすりがけはさぼります。
今回はブリムを有効にして印刷したので、スペーサーのような小さいパーツもきれいに印刷することができました。
ブリムというのは以下のような印刷物の周りについたスカートのようなサポート材のことです。
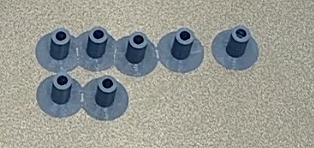
部品の底面の部分を拡張するように印刷されており、これでビルドプレートからはがれにくくしています。
ブリムを有効にするとビルドプレートとの接続が強固になるので、印刷時間を短縮することができます。
また加熱・冷却でゆがみがちな底面の形状を維持してくれるというメリットもあります。
印刷後の仕上げ作業(バリ取りみたいなイメージ)が多くなる、材料を若干多く消費してしまうという欠点がありますが、個人的には毎度有効にした方がいいんじゃないかと思ってます。
基板を筐体に組み込んでチェック
前回の記事で設計・組み立てを行った回路基板などを組み込んでテストしてみます。
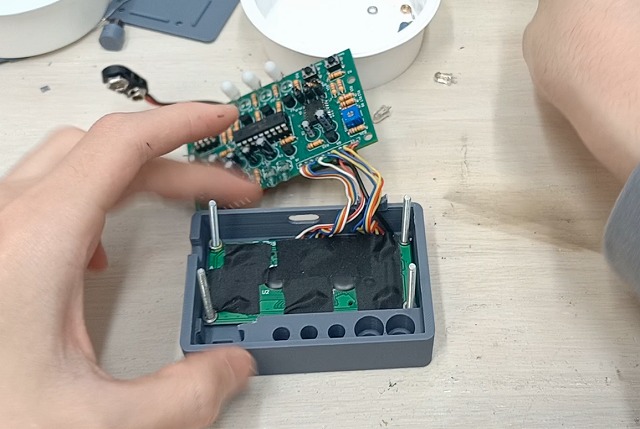
今回はLCDの配線や突起部分が干渉しないようにいい感じに加工したので、特に問題なく入りました。
本音を言えば、外周に突起のない平面的なディスプレイの方がいいんですが、値段が高くなるのであまり買いたくないです。
1602LCDは定番のディスプレイだと思いますが、1枚300円程度と激安です。
2年前くらいは1枚180円程度で購入できたので、ちょっと値上がりはしてきてますね・・・
キシダサァァアアアン!!!円安すぅううッ!!
今回は長ネジを使用した上の化粧板、真ん中の仕切り板、裏面の底板を一括して止める構造にしてみました。
ナットを回すのがめんどくさいので毎度ボックスドライバー欲しいなぁ~と思うんですが、長ネジだとねじの部分がボックスドライバーの内側につかえてどのみち使えないんですよね・・・
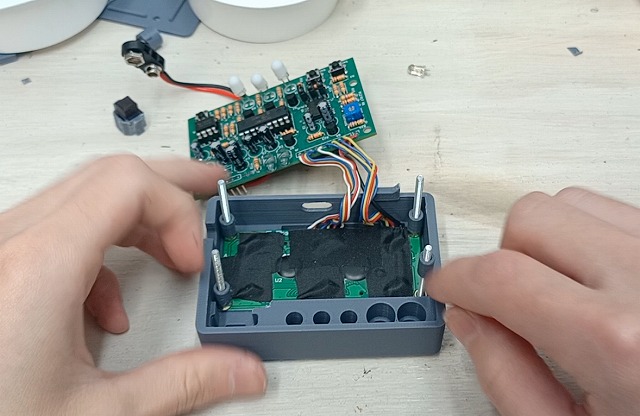
かといって短い木ねじタイプで母材にねじ切りしながら固定するには、3Dプリンタの印刷はあまりにもろいです。
何とかならんかなぁ~と毎度思っている気がしますが、いい感じの道具がなかなかないのが現状。
今回自作した基板はにはスルーホールタイプの背の高い部品がたくさんついているので、スペーサで高さをかせいでみましたが、割といい感じになった気がします。
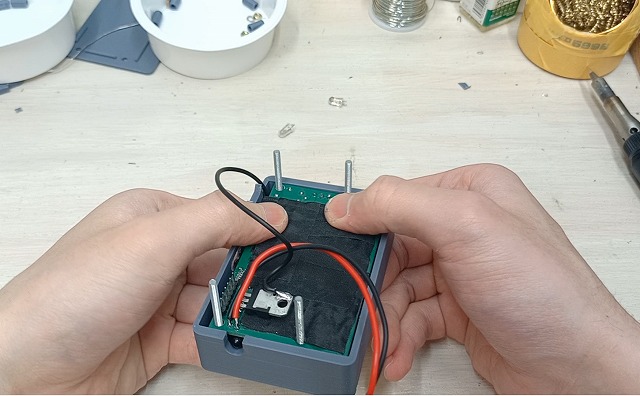
筐体側に基板をはめる枠を作ると組み立てが楽でいいんですけど、基板と筐体を同じソフトで作っているわけではないので寸法合わせるのが面倒なんですよね・・・
今回結構いい感じになったので、今後もスペーサーでいいかなぁと思いました。
余談ですが、スペーサーって結構するんですよね。
廣杉計器の白い六角スペーサが一番有名かと思いますが、一個20円くらいしたりします。
正直使い捨てぐらいの感覚で使いたいのものなので、3Dプリンターで印刷できるのは最高です。
筐体は3分割構造は割と良い
今回対して考えずに表面の箱、真ん中の部品整理用の箱、裏蓋の3分割構造にしてみましたが、割といい感じでした。
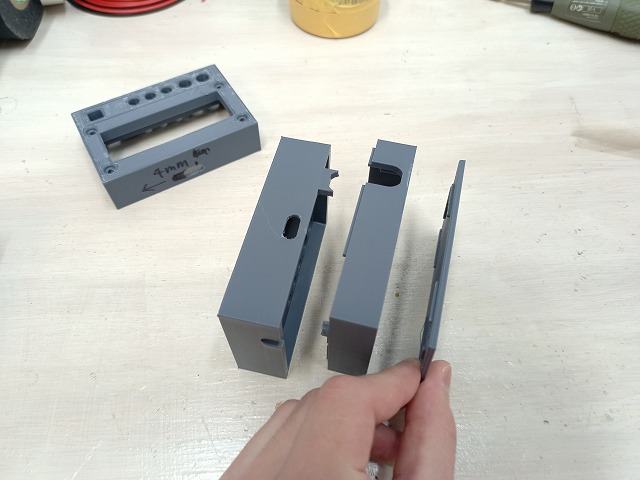
はめあい部分には小さい突起をつけて表面の箱と会うようにしてみましたが、パチッとはまるのでいい感じです。
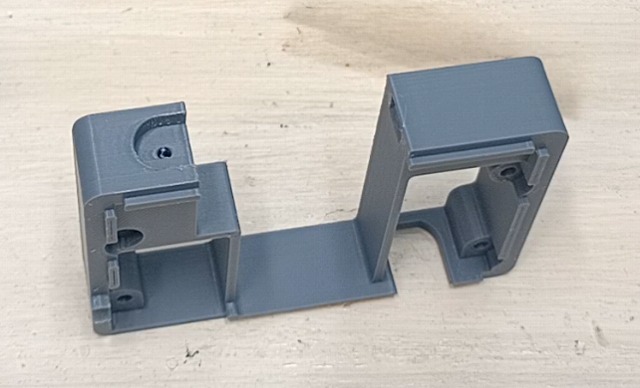
設計した際は表面の箱と真ん中の箱の溝の間の隙間を0に設定しているんですが、特に問題なく結合できました。
ちょっと固いところもありましたが、プラスチックなので力を入れればたいてい入っちゃいますね・・・・
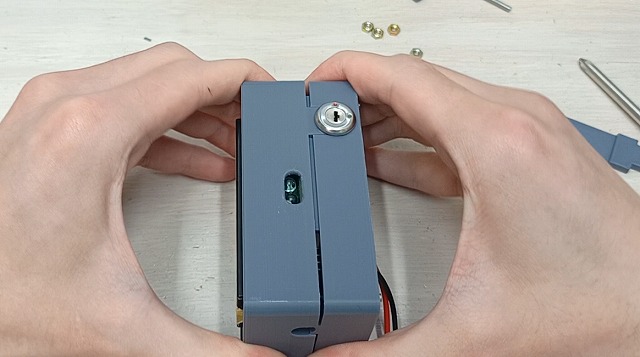
ボタンを作る
今回は赤外線信号コピースイッチ、赤外線信号送信スイッチ、赤外線信号送信周波数変更スイッチの3つのボタンがありますが、基板に直付けしているので表面までボタンが出てきていません。
なので3Dプリンターで印刷した延長パーツを使用して、奥にあるボタンを押せるようにしてみました。
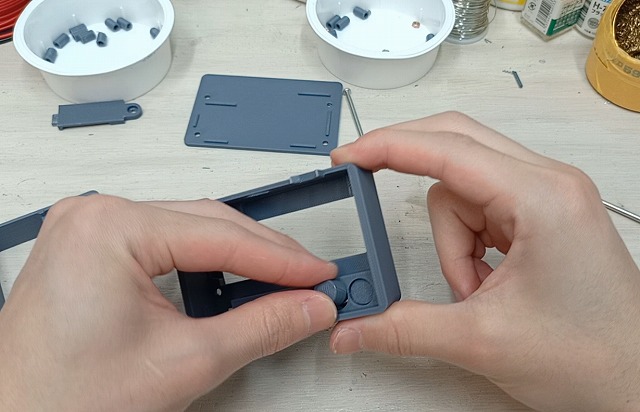
クリアランスは0.2mmにしてみましたが、丸いスイッチは結構いい感じです。
だが四角いスイッチが入らねぇ。。。。
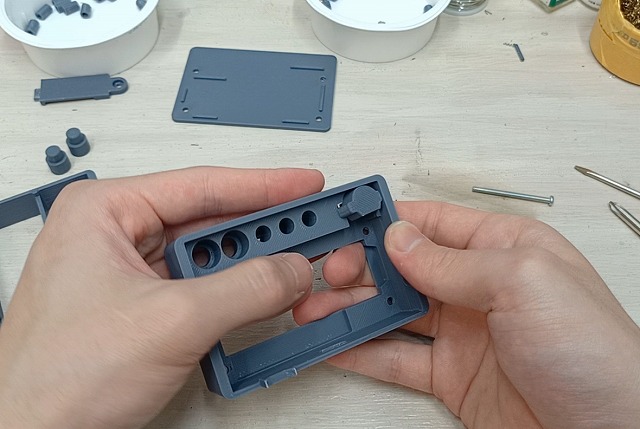
設計ミスで若干寸法が大きくなってしまったみたいです。
このサイズなら5分程度で印刷が終わるんですが、CADで修正して、エクスポートして、スライサーソフトで設定して・・・
というのがめんどくさいので無理やり加工します。

とりあえずはまるようになるまで削りました。
実は削りすぎてちょっと穴が開いてしまいました。
3Dプリンター中身が中空なので、後加工していると突然貫通して穴が開く、なんてことが多々あります。
実用には問題ないのでこのままいきます。
ボタンですが、筐体が同じ色だと目立たないので、黒色に塗ります。
色の異なるフィラメントで印刷しようと思ったんですが、フィラメント交換がめんどくさいんでやめました。
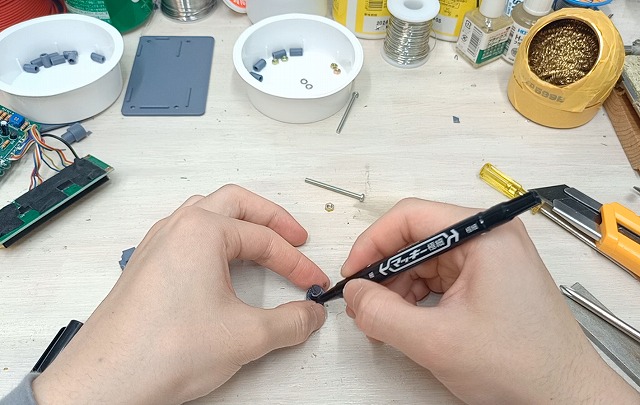
マイネームペンで塗ってそれっぽくして終わりです。
案外予熱したりチューブに材料通したりと手間が多いんですよね・・・・
将来的には3台ぐらいプリンターを置いてよく使う色を別々に印刷できるようにする予定。
オペアンプソケットが干渉してはいらないので加工
もう少しで終わりそうだったんですが、蓋を閉めようと思ったら閉まらない問題発生。
オペアンプの台座が干渉して基板がうまく入りませんでした。
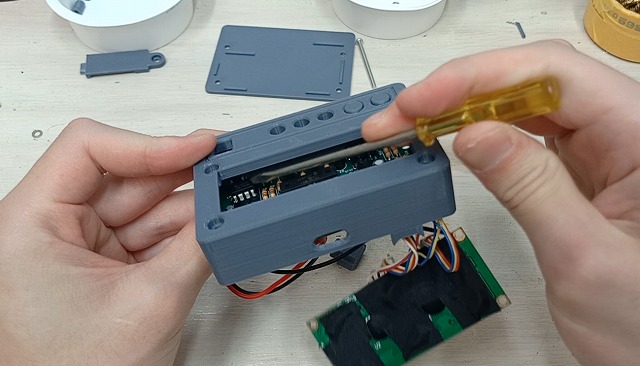
手前の箱は一番大きい部品のため、再印刷に結構時間かかりそうなのでニッパーで削りとることにしました。
慎重に、雑に削り取ります。
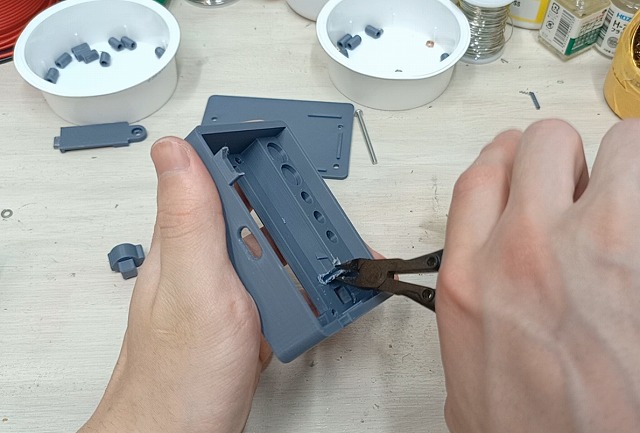
あまり後加工は増やしたくないのですが、外側からは一切見えないところなので妥協しました。
とりあえず基板が納まればOKとします。
LEDの位置を修正
タクトスイッチと同じですが、今回LEDも基板表面につけていました。
だいぶ奥まってしまって見栄えが悪いので、付け直すことにしました。
1cmくらい表に伸ばしてよく見えるようにします。
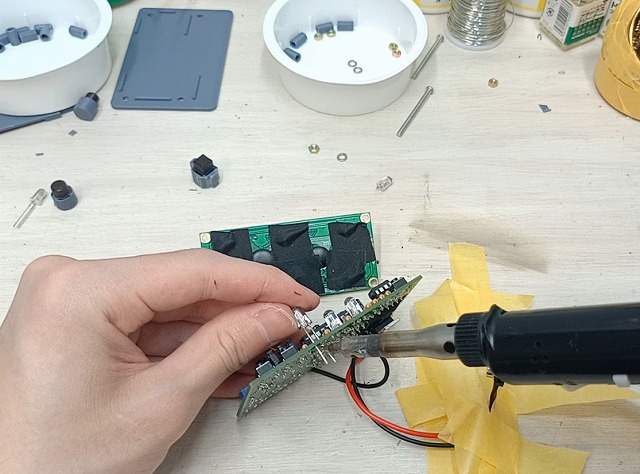
またLEDですが、今回散光キャップをつけることにしました。
今回使用したLEDはレンズが付いたタイプで、何かを照らしたりする用です。
今回はリモコンの情報を表示するために使っているので、ここまでまぶしい必要はないです。
手元に散光タイプの5mmLEDがなかったので、散光キャップをつけてごまかすことにします。
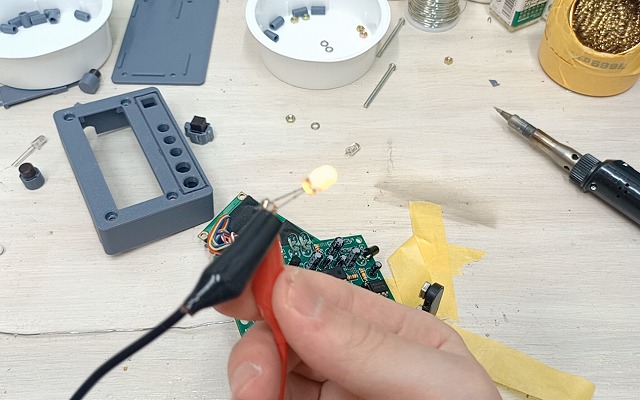
まぁまぁ良さそうです。
キースイッチ(無駄)を取り付ける
次に電源のON/OFFをつけるためのキースイッチを取り付けます。
別にスライドスイッチで良かったんですが、ねじ込み式で取り付けやすいのとネタになるのとでキースイッチを採用。
完全に無駄です。
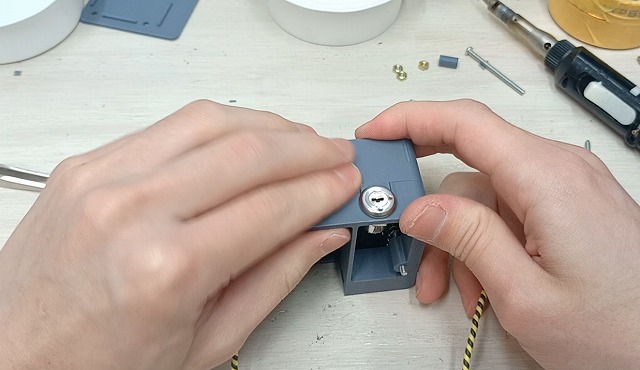
小さいですが、一応鍵以外では回らなかったりと、よくできています。
セキュリティ(仮)ということで採用。
電源部にダイオードを取り付ける
最後のはんだ付けです。
9V電池から基板への接続の間にダイオードを入れることにしました。
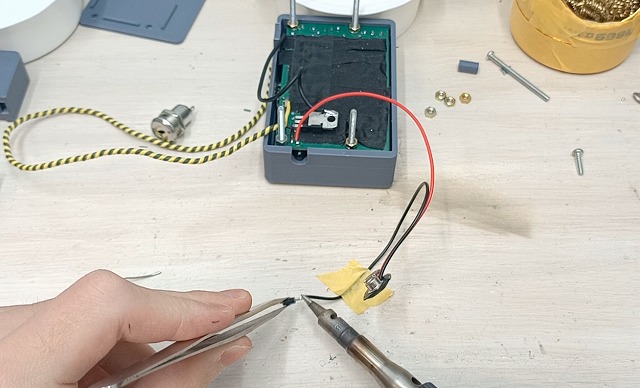
動作テストしているときに電池の極性を逆にして触れてしまい、マイコン(260円)が死にました。
ちょっとなら大丈夫かな~とかおもったんですが、割と簡単に逝きます。
今後も電池交換のたびにやらかしそうなので念のためつけておきました。
ダイオード自体は0.7V程度の電圧降下がありますが、特に電流が流れる回路ではないので発熱はしないと思います。
電源電圧自体も 0.7V 減ってしまいますが、そもそも今回はレギュレータLM7805を使って 電池:9V → マイコン電源:5V に降圧しています。
レギュレータは一般的に入力と出力の電圧差が小さいほど発熱が小さくなるので、今回は良い方向です。
特に問題ないので1A程度の汎用整流用ダイオードを取り付けました。
裏蓋を取り付ける
最後に裏蓋を取り付けます。
今回は先ほど取り付けたキースイッチのせいで、はめ込む際のガイドとナットが干渉してフタが閉まりませんでした。
新しく印刷するのは面倒なのでカッターで削りました。
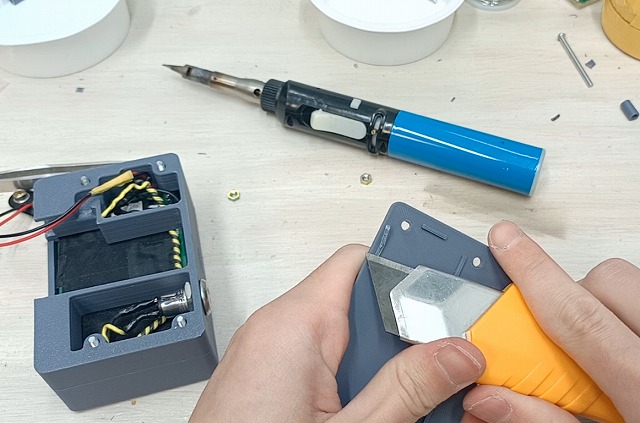
が、誤って反対側のはめ込みガイドを削ってしまいました。。。。
両方ともガイドがなくなってしまったのでもしかしたら裏蓋がずれてママ閉まってしまうかもしれませんが、ちゃんと位置合わせすれば多分大丈夫、と信じたい。
とりあえず干渉する部分はなくなったので、蓋を占めてナットで固定します。
ボックスドライバーが欲しい(再)・・・・
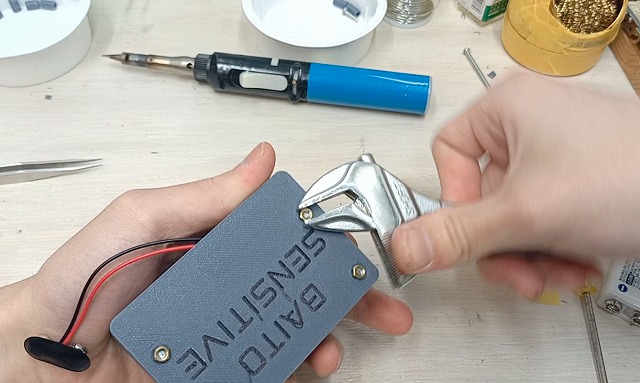
電池ボックスのフタをテスト
今回は電池ボックス的な空間を作ったので、いちいち筐体をばらさなくても電池交換が可能です。
正直電源スイッチがあるので電池が勝手にどんどん減ってくことはないです。
わざわざ蓋を別に作る必要もないかなとは思ったんですが、完成度が上がりそうなのでやってみました。
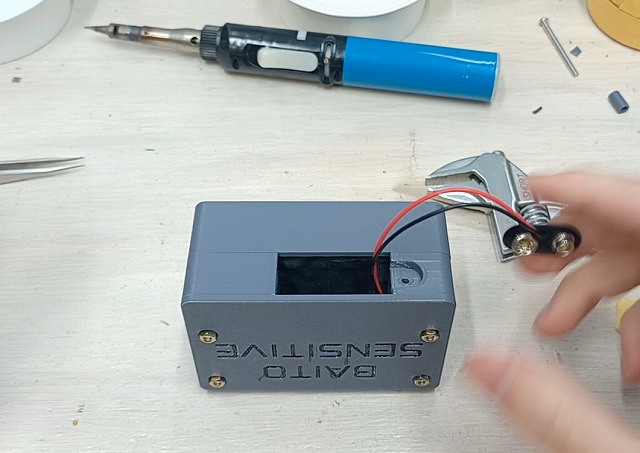
電池交換用のフタはしょっちゅう取り外しするものなので、0.1mm寸法が小さくなるように設計したんですが、差し込むツメの部分だけ忘れていました。
ここも入らなかったので後加工。
3Dプリンタの印刷物は中身が中空で・・・と何度か書きましたが、実は小さめの部品は材料の充填率が高めになるので、多少削っても穴が開いたりはしないです。
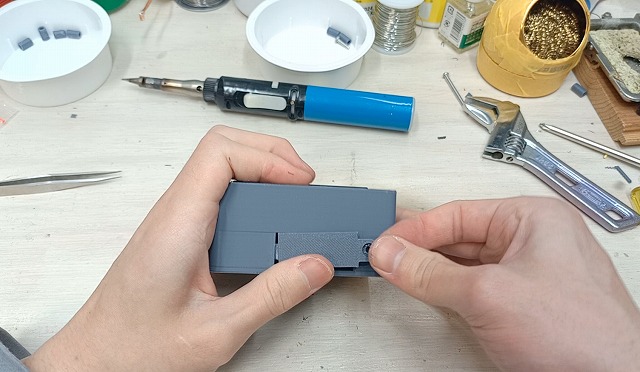
とりあえずしまったのでOK。
作業終了です。
完成☆
何とか完成しました。
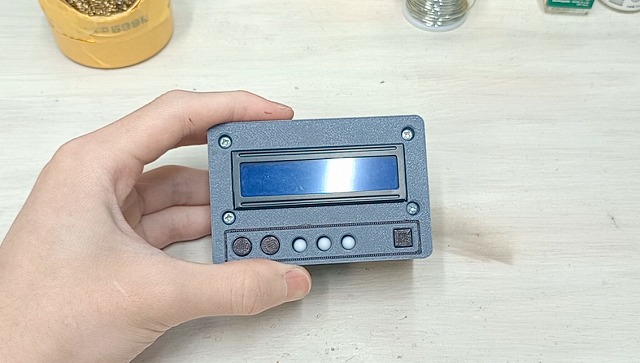
思っていたより後加工が多くて手間がかかりましたが、一から材料加工して作るよりは圧倒的に速いです。
3Dプリンター様様ですね・・・・(感謝)
まとめ
今回は筐体作成、加工、最後の部品追加を行いました。
細かいところでミスはありましたが、割といい感じに仕上がった気がします。
次回は完成品の動作、チェックをする予定。
プログラムの方も若干バグが残っているのでいい感じに修正する予定です。
それでは、また。
ここまでの記事
-
-
【自作】PICマイコンで赤外線学習リモコンを自作する①:試作基板作成
Youtube動画上げたいな~とか言い出して3本上げたら1年たってました。 三日坊主、極まれり。 今回は最終的に動画にまとめてみました。 学習リモコンを自作する 今回やってみるネタは学習リモコンの自作 ...
続きを見る
-
-
【自作】赤外線 学習 リモコン のつくり方を紹介する ②:赤外線通信の解析とソフト設計
前回は赤外線を受信・送信するために最低限必要なハードウェア(マイコンボード)を試作しました。 今回は赤外線の送信・受信を実際に行うために必要なプログラムを作成し、マイコンボードに書き込んで動作テストを ...
続きを見る
-
-
【自作】PICマイコンで赤外線学習リモコンを自作する③:基板設計・組み立て
前回までで試作したマイコンボードを用いたソフトの作成・デバッグが完了しました。 完全にバグは消えていませんが・・・・・ 今回は試作した基板を参考に、から完成形の基板を作っていきたいと思います。 基板を ...
続きを見る
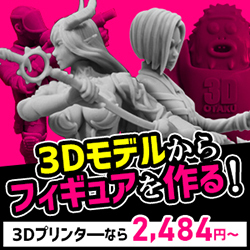